How NIMO's drying cabinets are tested and optimized
Behind every drying cabinet from NIMO lies extensive work where technology, innovation, and testing come together. Through meticulous testing and close collaboration between departments, we ensure that the products meet high standards for performance and energy efficiency.
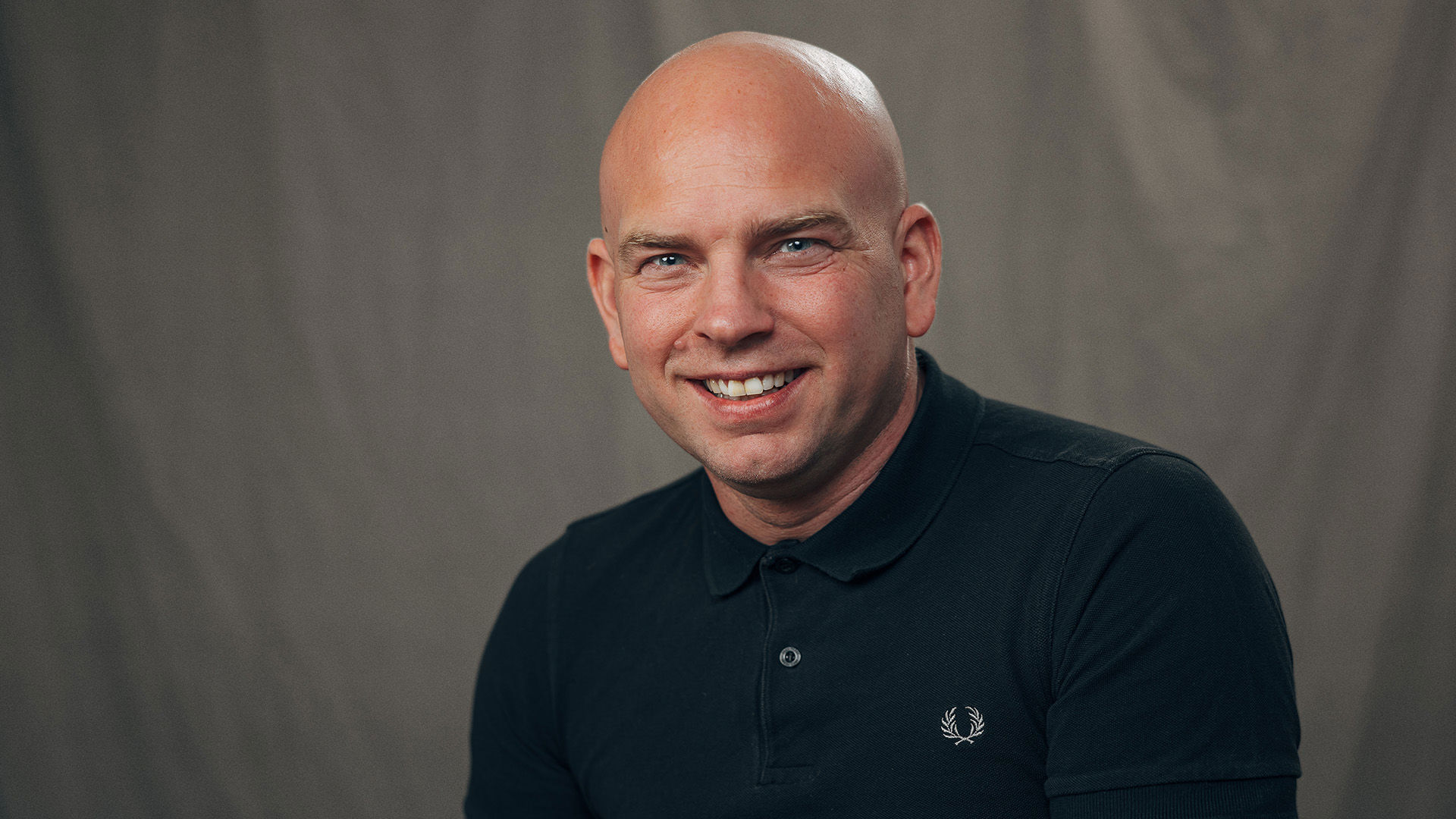
From lab to finished product
Gustav Bertilsson, product developer at NIMO, is one of the key people in the development process. His work begins when the design and innovation department, or sometimes the production and marketing teams, provide clear directives on what needs to be validated. This initiates a structured workflow where every component and function is analyzed and evaluated.
– We look at the market specifications and base our work on those requirements.Then, we conduct tests in various environments to measure drying capacity, energy consumption, and other vital parameters. This includes weighing laundry, hanging it for drying, and measuring how much water is removed over time, explains Gustav.
Tests to ensure quality and performance
At NIMO, everything from the functionality of heat pumps to the energy consumption and capacity of the products is tested. A significant part of the work involves measuring and analyzing data to optimize performance. Temperatures, pressures, and overheating are carefully monitored to ensure that each product meets the company’s standards.
– Most of the process is about achieving the correct performance according to the specification requirements and finding the right environment for testing. For example, we measure how much water is removed from the laundry per minute and how long the programs take. We also analyze power consumption to ensure energy efficiency, says Gustav.
When problems or deficiencies are identified, they are addressed quickly. Simple adjustments are made directly in the lab, while more complex issues are referred back to the design or marketing teams for further development.
Alizé Steaming Cabinet
One of NIMO’s latest additions, the Alizé Steaming Cabinet, is a clear example of how systematic testing forms the foundation for a product’s success. The cabinet's steaming capacity and hygiene programs have been fine-tuned in the lab to ensure optimal results while being as gentle as possible on textiles.Tests conducted by RISE Research Institutes of Sweden show that Alizé can eliminate up to 99.9999999% of viruses such as SARS-CoV-2 (Covid-19) and Norovirus.
Cross-department collaboration
One of the most important aspects of the testing and development process is the collaboration between different departments. In close dialogue with design, production, and procurement, product developers like Gustav work to ensure that the products not only meet expectations but are also continuously improved.
– I often participate in meetings with suppliers to discuss test results and how we can improve the products. Sometimes, we also make real-time adjustments in the lab, says Gustav.
Focus on innovation for the future
With a clear ambition to stay at the forefront, NIMO continues to evolve.
– Heat pump technology has truly taken us far in terms of energy efficiency and performance. It’s inspiring to see how our testing activities and innovations contribute to creating better products for the future, concludes Gustav.